What Composites Do for 3D Printing
Composite fibers boost specific properties of traditional 3D printed parts - usually strength, stiffness, heat resistance, and durability. This gives them a strength advantage over more traditional thermoplastics used in 3D printing like ABS or PLA, so the applications of 3d printing can expand with these additional materials and the properties they bring to the table.
Thermoplastics are plastics that can change state without a change in chemical properties. This makes them popular 3D printing materials because they can easily be melted, extruded layer by layer, and immediately cooled into a shape. However, the properties that make them good for 3D printing make them a poor fit for engineering-strength applications - many of these thermoplastics have a relatively low melting point and aren’t very strong or stiff.
Composite materials, on the other hand, are parts made up of more than one material that, when combined, have properties different from their original materials. Materials like concrete and particleboard can be considered composites, because they are mixtures of a variety of materials. However, when we talk about composites from an engineering standpoint, we usually refer to composites with reinforcing fibers. Carbon fiber, fiberglass, and Kevlar are three of the most common fiber materials used for composites in industry. As we covered in the Physics of 3D Printing, the fibers are like spaghetti - thin, brittle, and easy to snap if bent. These fibers are almost never used by themselves - they are woven into sheets, wrapped into rods, or formed into custom molded shapes with the help of a matrix material to harden the fibers into an optimized shape. When many fibers are bound together to create larger structural elements, forces can distribute and disperse loads along the lengths of all of the fibers.
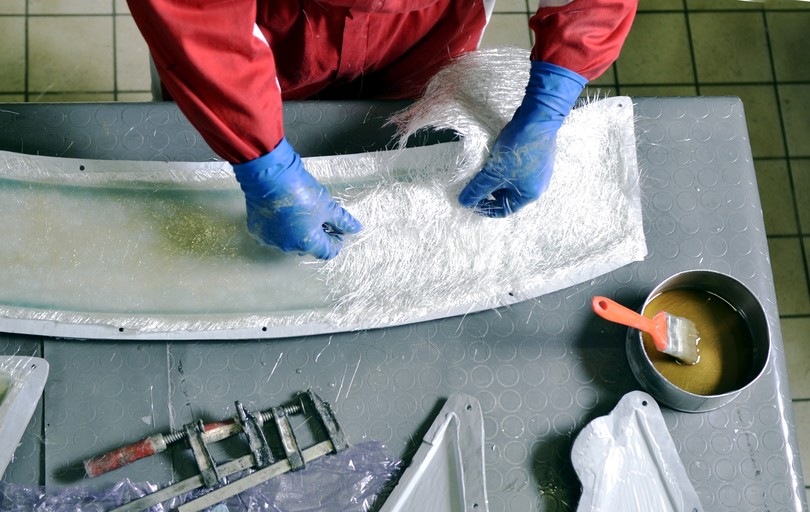
Fiberglass strands being laid down in a mold and cured with a thermoset resin.
Carbon fiber has one of the highest strength-to-weight ratios out there, making it very valuable for creating lightweight, strong parts. The fibers themselves are made up of carbon atoms whose crystal structure is aligned into strands, making the strands incredibly strong in tension. Traditionally, thermoset resins are used as the bonding agent to set these fibers into a designated shape, cured around a matrix material like foam. So you can create a sandwich panel by “sandwiching” the foam between to sheets of fiber weave, and curing it all with resin. In the context of 3D printing, the fiber can take two different forms:
Chopped Fibers are short-length fibers chopped into segments less than a millimeter in length and mixed into traditional thermoplastics to form what is called a filled plastic. These can be printed with an FDM printing process.
Continuous Fibers require a slightly different 3D printing method, in which continuous fiber strands are coated in a curing agent and laid down into a thermoplastic matrix extruded via a secondary print nozzle. This process is called Continuous Fiber Fabrication (CFF).
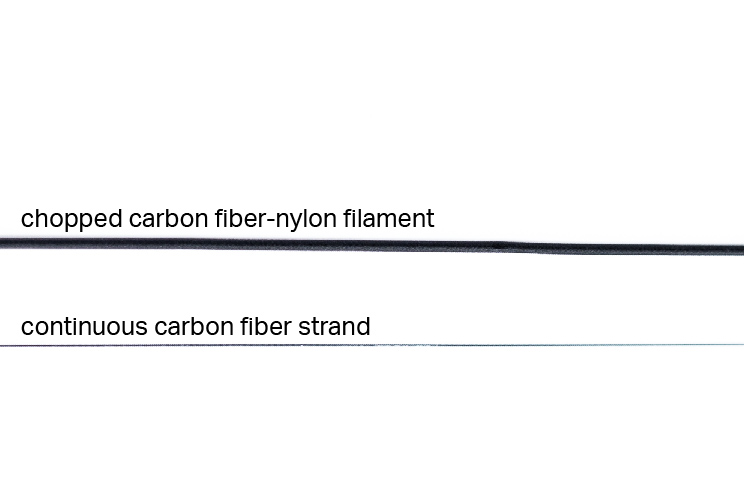
Either way you add fiber, the addition of the fibers boosts part strength and other material properties, but the amount it helps differs depending on the way that fiber is used, and what fiber it is. Generally speaking, a continuous carbon fiber 3D print is stronger than chopped carbon fiber 3D because the continuity distributes any applied loads.
Chopped Fiber 3D Printing Materials
Chopped fiber filled plastics are the most common type of composite 3D printed plastics. The most widely used chopped composite 3D printing material is chopped carbon fiber - where carbon fiber pieces are mixed with traditional 3D printing plastics like nylon, ABS, or PLA. Adding this “filling” to thermoplastics is a material booster pack. The fibers take on some of the stresses of the part, like how concrete is added to cement to boost its strength. The fibers handle some of the applied stresses on the part, boosting the properties of typically lower-grade materials.
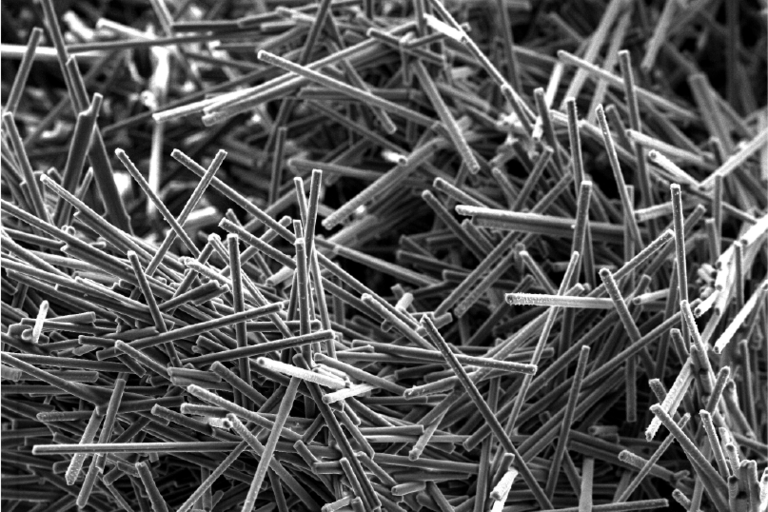
A close-up of chopped carbon fibers used in 3D printing, taken on an SEM.
These fibers are chopped up into fine pieces and mixed into the plastic before it gets extruded into a spool for use with material deposition-based 3D printers. In this case, the 3D printing process remains the same, because the fibers are just suspended in the thermoplastic - so it gets heated, extruded, and cooled into the part just like any other FFF style 3D printed. Chopped composite 3D printing materials takes normal plastic that may be lacking in certain properties and boost it. In the case of carbon fiber, the fibers boost the strength, stiffness, and dimensional stability of the part to make it higher-performing than its base plastic.
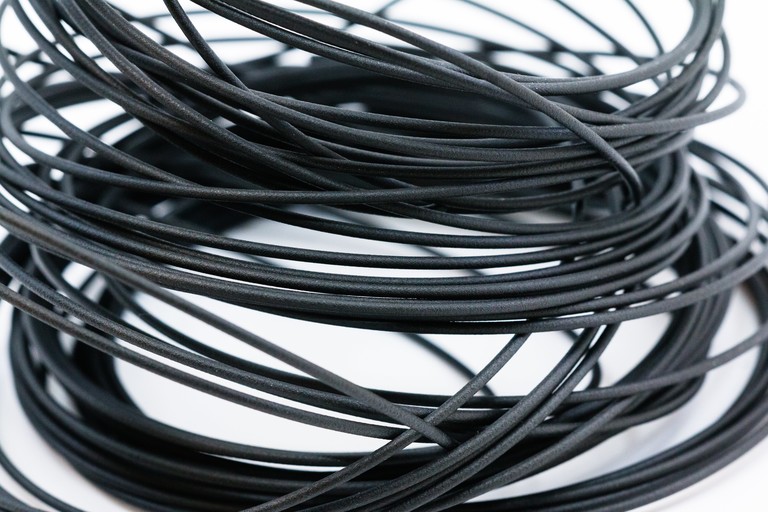
Chopped carbon fiber 3D printing materials can be used like normal 3D printing plastics, boosting some material properties.
The quantity of fibers and the length of chopped segments impacts the strength and quality of the part. Different vendors blend different amounts of fiber into their plastic, yielding materials with different strengths. Below a certain threshold, and the fibers boost surface finish, print quality. Above that threshold, mixing in a large quantity of longer fibers, and you get a stronger material, but you sacrifice surface finish and part accuracy because there is a smaller percentage of plastic in the material overall. The thermoplastic is essential to the mixture because it makes the printing process work well, so your parts can only get so strong.
Continuous Fiber 3D Printing
Continuous fiber 3D printing adds continuous strands of fiber reinforcement to the part (think back to fiber strands), to achieve metal-strength properties at a fraction of the weight. Using two print nozzles, the printer builds the matrix material out of a thermoplastic, and irons down continuous strands of continuous fibers into the part. This process is called Continuous Fiber Fabrication (CFF).
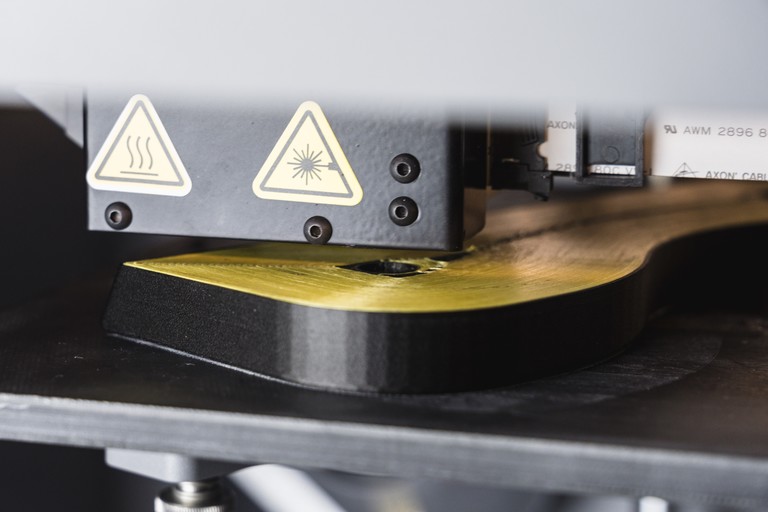
Continuous Kevlar strands are ironed into this part to increase its impact resistance with a composite fiber printing nozzle. A thermoplastic matrix material forms the skin and core of the part.
The power of CFF comes from the continuity of the strands. Unlike chopped fibers, continuous strands can absorb and distribute loads across their entire length. When placed within a thermoplastic matrix, the part can handle higher loads and absorb larger impacts. This allows these parts to achieve the strength of metal at a fraction of the weight.
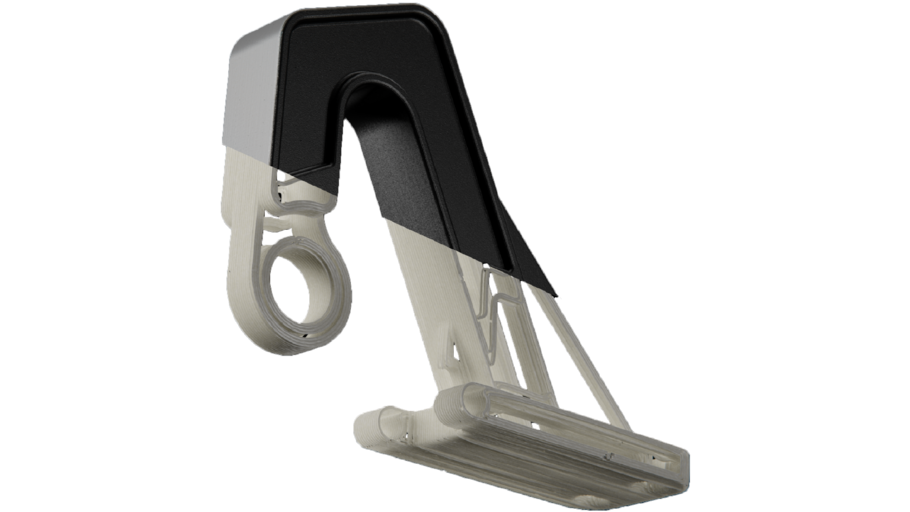
Continuous fibers form the backbone of a 3D printed part, because the loads distribute along their length, rather than into the plastic.
The CFF 3D printing process consists of two steps per layer - first, a thermoplastic is extruded to form the infill and shells of the part - this serves as the “matrix” material of the composite. Next, the continuous fiber is ironed into that matrix, fusing with the thermoplastic by use of a compatible resin coating. This process repeats layer by layer, forming the fibers into the backbone of the 3D printed part, while the thermoplastic acts as a skin. This process is also similar to how rebar can be laid down inside concrete to reinforce it.
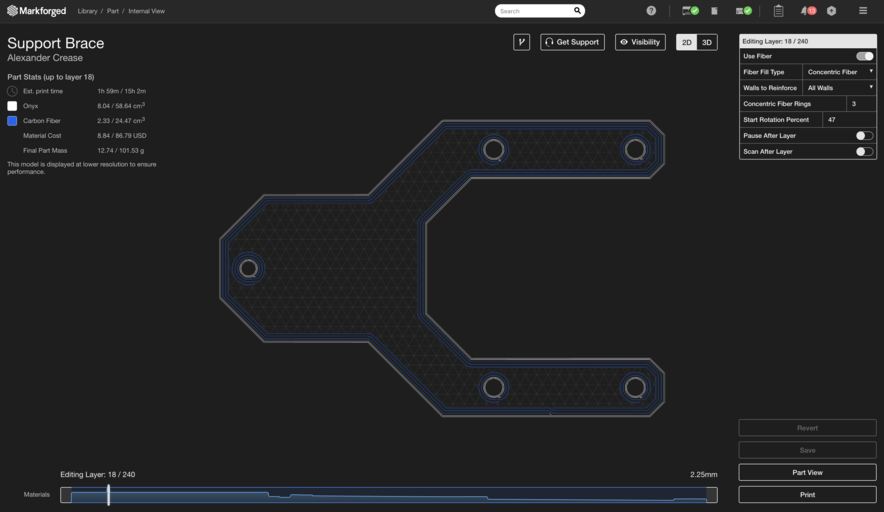
The fibers form the "backbone" of the part and can be laid down in specific patterns to optimize a part’s strength for its weight and material consumption. You can place fiber in specific areas based on how the part will experience load, putting the strength exactly where you need it. This is very different from standard deposition-based 3D printers, including with chopped fibers, because these methods have an even distribution of properties throughout the entire part. Different fiber reinforcement options can be used for different loading conditions and behaviors. You can learn more about the different reinforcement strategies in Fiber Reinforcement Strategies.
A variety of different fibers can be used for reinforcement as well, depending upon what material properties your part needs to have. Markforged 3D printers offer a few different fiber materials so that you can choose the strength behavior of the reinforcement:
Carbon Fiber is a stiff and strong fiber that behaves like 6061 Aluminum, so it can be used for lightweight components that support heavy loads.
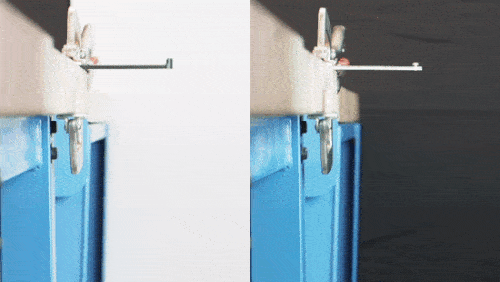
This 3D printed carbon fiber can match the strength of aluminum when continuous. Both are supporting a 27.5 lb load.
Fiberglass is a sturdy, cost-effective reinforcing material with some compliance to it. It boosts part strength above that of plastics and is a good starting point for printing with reinforcement.
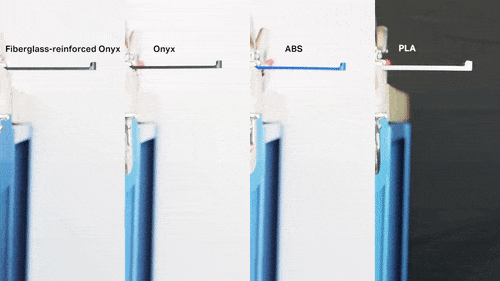
Fiberglass is a robust 3D printing fiber option, exceeding the strength of chopped fiber, ABS, and PLA when supporting a 7.5 lb weight.
Kevlar has high toughness and shock resistance, making it ideal for shock-loading and high-impact conditions. It bends instead of breaking.
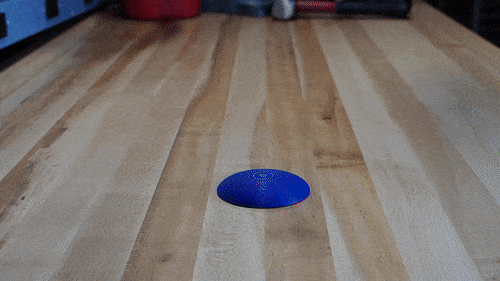
PLA, ABS, and Kevlar reinforced 3D printed parts getting shock-loaded with some big hammer hits!
High Strength High Temperature (HSHT) Fiberglass maintains its strength and stiffness at high temperatures because of its high heat-deflection temperature. Its heat resistance allows it to hold up in more extreme environments.
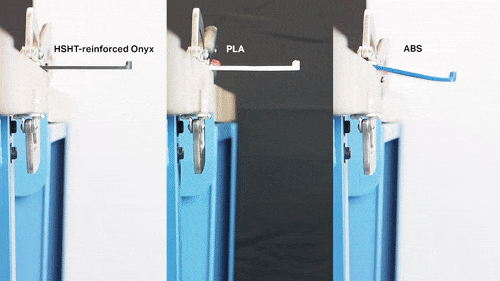
This test was performed after heating each beam to 300 degrees Fahrenheit in an oven. HSHT does not lose strength at high temperatures, so it still supports the 5 lb load.
So between selecting different fiber types for certain material needs, and controlling where the fiber can be placed layer by layer, you can control the behavior and performance of your parts. This is one of the primary advantages continuous 3D printed composites have over chopped fiber materials. Not only do you get stronger parts, but you also can produce parts optimized for their application.
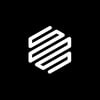
Written by Markforged
Markforged is transforming manufacturing by addressing 3D printing as a holistic problem. Their process innovations are only possible by a combined effort in advanced cloud computing, cutting-edge materials science, and industrial design.