Both 3D printing technology and composite materials, especially carbon fiber, are big players in the world of prosthetics, and with the Mark One 3D printer, students at Auburn University have designed and prototyped unique concepts in the field of accessible devices. Jerrod Windham, associate professor of Industrial Design in Auburn’s School of Industrial and Graphic Design, leads a class that is part of a project nine years in the making. Each semester, rehabilitation and industrial design students work with client users with physical disabilities to develop specific products that target their needs or desires as individuals.
“Our goal at the beginning of the semester is to work with a client user and by the end of the semester hand off a piece of technology that will work for them,” Widham explains. This year’s projects focused on working to enhance the lives of people using prosthetic devices. From common challenges like helping those with leg prosthetics put on a pair pants, to more specific cases like helping a woman with a shoulder disarticulation play the cello, the materials and applications that challenge these students range far and wide.
3D printed shoulder plates for a woman who wanted to play the cello again.
3D printed prosthetics allow for ease of customization, iteration, and form fitting. Industrial strength 3D printing materials like the Markforged nylon filament provide a durable, long lasting solutions.
The Mark One sits in their lab among a range of unique 3D printers with different capabilities, and it stands out for its fiber reinforced plastics and the strength to weight ratio of its parts. “Some of these smaller 3D printed prosthetic devices were not as durable as they need to be, which is why we usually see 3D printing more in the world of prosthetic hands than legs and feet,” Windham described. “The strength to weight ratio was important to us: we were trying to create a structural element on a 3D printer that was capable of holding the weight of a human being.” Prosthetic devices require lightweight materials that can hold the weight of a person, which is why carbon fiber prostheses are popular in the field. Carbon fiber 3D printing with the Mark One provided a great overlap of the two fabrication methods. Apart from the strength of their parts, the Mark One provided a surprising advantage with wearable tech. When working with the soon-to-be cello player, they needed to fit the wearer’s shoulder blade to their prototype prosthetic. “We were able to scan in her shoulder and body and utilize software to build a shell that covered her shoulder and a portion of her chest and shoulder blade. If we were to do that out of PLA or ABS, it would be to brittle and would probably degrade a lot quicker.” With Markforged nylon, the team was able to design a device that could flex enough to conform to her body comfortably.
The shoulder plate and joints were 3D printed on the Mark One due to its durability, flexibility, and comfort.
Despite a shoulder disarticulation, students used 3D printed prosthetics to help people pursue passions they thought they had to leave behind.
“The device we created for the woman with the shoulder disarticulation…she’s able to hold a bow and articulate the arm in a way that it’s able to run across the strings…she hasn’t played the cello since she was a child but it’s something she really wanted to do again,” Windham explained. Every person the students have worked with has a unique need that they value. A father missing three fingers wanted to shake people’s hands and play baseball with his son. An amateur fisherman wanted a water resistant fairing to protect his prosthesis while near the water. These students have been giving meaning back to the lives of individuals, and not in the form of quick prototypes. The durability and the strength of the 3D printed prosthetics they are making allow these students to provide lasting solutions to the people they work with.
The durability and flexibility of the hand made it a good fit and a long term solution to the problem.
One of the products students produced on the Mark One enabled a man to shake hands and cast a good first impression again.
“Durability was a question. It was a big concern, especially if you’re handing stuff off to children. Markforged has given us confidence to pursue this as a legitimate means of fabricating prosthetic devices…a real long term solution.” – Jerrod Windham
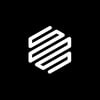
Written by Markforged
Markforged is transforming manufacturing by addressing 3D printing as a holistic problem. Their process innovations are only possible by a combined effort in advanced cloud computing, cutting-edge materials science, and industrial design.