This article highlights best practices when printing with Onyx ESD. For more information on material properties, see the Onyx ESD material information support article
Loading Onyx ESD
Onyx ESD is more brittle than Onyx. To avoid breakage during the loading process, take care not to bend Onyx ESD filament when feeding it through the drybox adapter, into the plastic feed tube, and into the plastic extruder. We recommend that you pull the feed tube away from the extruder to create a straight path from the feed tube to the extruder inlet.
After successfully loading Onyx ESD, ensure that the filament is not tangled in the drybox to prevent reduced print quality.
Printer Hardware Setup
Onyx ESD has less bed adhesion strength than Onyx, so it is especially important to maintain a level print bed by taking the following steps:
- Run the Laser Bed Level utility before each print
- Ensure that the Scan Bed Before Prints toggle switch is enabled on the System Info screen (Menu > Settings > System Info, then select the gears icon in the bottom row)
Regardless of your material selection, we recommend that you clean the plastic and fiber nozzles with a brass brush prior to printing parts. Regular nozzle maintenance reduces material buildup that can lead to degraded part quality.
Print Bed Setup
Since Onyx ESD has less bed adhesion strength than Onyx, it is important to apply two layers of glue before each new print in order to prevent warping – the first with horizontal strokes and the second vertical. Make sure to cover the entire print area, along with the purge line and bed scan areas.
Note that Onyx ESD's wet plastic purge line -- the thicker purge line -- prints in a new sinusoidal pattern. The new purge line should not require more material than the previous straight purge line. The thinner purge line for drying material is unchanged.
Slicer
Creating an Onyx ESD part in Eiger is largely the same as with any other material. At this time, only the 0.100mm and 0.125mm layer heights are available for Onyx ESD.
Some feature-specific notes are listed below:
- If you are concerned about the part warping off of the bed, consider enabling the Use Brim toggle switch
- If the bottom of your part (i.e. the first layer on the bed) is not conductive enough, consider using the Raise Part feature, as it has been shown to significantly increase the conductivity of the first layer
- Note that Solid Fill is the most likely infill selection to exhibit part warping and bed adhesion issues; use with caution
During the Print Job
When printing with Onyx ESD, ensure that the printer lid and visor stay closed throughout the entire print. Preliminary observations show that opening the visor or lid while printing Onyx ESD can negatively impact surface finish.
Consider limiting the number of pauses you insert into Onyx ESD parts, since pausing Onyx ESD prints will likely lead to a drastic change in surface quality at the layer of the pause.
Support Removal
The relative stiffness and brittleness of Onyx ESD means that extra care should be taken when removing supports. Where standard Onyx would typically "accordion" during support removal, certain Onyx ESD geometries may break, making removal more challenging. Pull less aggressively on the support accordion to ensure successful support removal.
Removing support material from small holes is more challenging with Onyx ESD. However, using the right tools, such as a punch or pick, will make the task much easier. The image below shows support removal using a pick.
Printing Onyx ESD and Nylon White on the Same Printer
When switching from Onyx ESD to another material, be sure to purge all residual Onyx ESD from the system. For other print materials, a standard purge line typically removes all residual material, but Onyx ESD may require additional purges. If you are switching to another material and require it to be entirely free of Onyx ESD, we advise that you run the purge line two times.
The image below shows a progression of purge lines when switching from Onyx ESD to Nylon White: residual contaminants in the left and center purge lines, and a clean Nylon White purge line on the right.
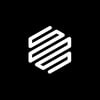
Written by Markforged
Markforged is transforming manufacturing by addressing 3D printing as a holistic problem. Their process innovations are only possible by a combined effort in advanced cloud computing, cutting-edge materials science, and industrial design.