In the modern manufacturing landscape, the quest for materials that combine the lightweight benefits of plastics with the strength and durability of metals is ever-present. This is where the Markforged FX10 and FX20 come into play, bridging the gap between metal and plastic through innovative composite printing. These advanced 3D printers stand out for their unmatched ability to produce robust, high-quality parts that meet demanding industrial needs. Here’s how the FX10 and FX20 can streamline your operation from prototype to production. Fostering innovation, shortening the development time frame, reducing costs, and position manufacturers as leaders in their industries.
Key Features of the Markforged FX10 and FX20
- Continuous Fiber Reinforcement (CFR): The Markforged FX10 and FX20 excel in composite printing due to their patented Continuous Fiber Reinforcement technology. This feature embeds long strands of carbon fiber, Kevlar, or fiberglass into printed parts, resulting in components with a strength-to-weight ratio that rivals aluminum. Manufacturers can now produce parts that are as light as plastic yet strong enough for their application.
- Build Volume: The FX20 offers an impressive build volume of 525 x 400 x 400 mm, allowing for larger parts and assemblies to be produced in one print. The FX10, while more compact, still provides a 375 x 300 x 300 mm build volume, ample space for mid-size, high-strength parts. This flexibility empowers companies to create everything from custom fixtures to fully functional, load-bearing components.
- High-Temperature Printing: The FX20 is designed for printing high-performance thermoplastics. ULTEM™ 9085 is known for its exceptional strength, heat resistance, and chemical stability. Vega (a PEKK based filament) is a great combination of strength, toughness, chemical resistance, and low flammability. This allows manufacturers to confidently produce parts for aerospace, automotive, and other sectors where thermal and mechanical performance are critical.
- Production Printing: Both the FX10 and FX20 were designed for reliable, lights out printing around the clock for days on end. The FX 10 has four 800cc material bays, high print volume or long print runs automatically load material from the next available bay. The FX20 also has two 3200cc bays for the same purpose.
- Superior Software Integration: Both printers are seamlessly integrated with Markforged’s cloud-based Eiger software, enabling precise part design, print scheduling, and material management. Eiger’s intuitive interface makes it easy for every engineer to optimize part strength by strategically placing continuous fibers only where needed. Reducing part weight and costs a double payback.
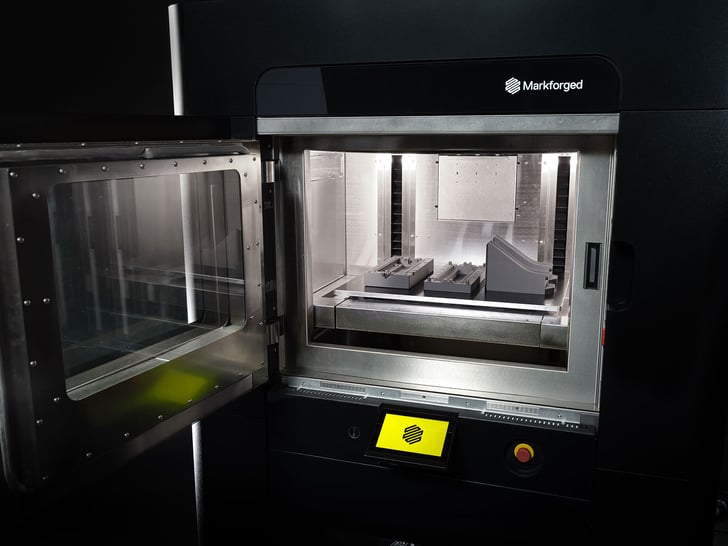
Why Choose the FX10 or FX20 Over Complex Metal Printing Systems
Lower Equipment and Maintenance Costs
Traditional metal printing systems are a significant financial investment. It is not just the machines themselves, it's the associated facility updates, training, and operational and maintenance overhead. The FX10 and FX20 offer a cost-effective alternative, minimal facility updates, lower annual overhead costs all while delivering exceptional plastic composite parts..
Simplified Setup and Operation
Metal printing systems often require specialized knowledge and extensive setup times. Then a machining process to remove supports. The FX10 and FX20 were designed for ease of use, allowing engineering teams to be trained and ready to operate quickly. The streamlined Eiger software further simplifies the process, enabling everyone on the team to start producing high-strength lightweight plastic composite parts right away.
Reduced Safety and Environmental Concerns
Metal printing systems often involve high-energy lasers or electron beams, presenting many potential safety hazards and requiring specialized ventilation systems. Not to mention all the personal gear required to safely handle the metal powders. The FX10 and FX20 were designed to operate right in the engineering department if needed. The FX 10 just plugs into a 110 outlet. Where the FX20 with the higher heat materials requires 3 phase power drop.
Comparable Strength and Lightweight Properties
With the capability to embed continuous fibers like carbon fiber, the FX10 and FX20 can produce parts with a strength-to-weight ratio similar to that of aluminum, making them ideal for applications where weight reduction is crucial and strength cannot be compromised.
Faster Production Times
Metal printing systems may require post-processing, such as machining or sintering, which adds time and complexity to the manufacturing process. The FX10 and FX20 streamline production with minimal post-processing, allowing manufacturers to go from CAD to finished part faster. Depending on printer demand maybe even same day.
Design Freedom
Metal printing systems can sometimes limit design possibilities due to support structures and heat concerns. The FX10 and FX20, however, give engineers more design flexibility, enabling intricate geometries and strategic fiber placement that optimize part performance.
Resource Efficiency
Metal printing can produce significant waste from support materials to rafts to control shrinking. That's not even factoring in the geometry that everyone thought would work but just doesn’t. The FX10 and FX20’s continuous fiber printing ensures that material is only used where it’s needed, significantly reducing waste and improving sustainability.
Tips for Maximizing the Potential of FX10 and FX20
- Optimize Fiber Placement: Use Eiger’s advanced tools to analyze load paths and reinforce only critical sections of your parts. This approach minimizes material use and shortens print times without sacrificing performance.
- Embrace Rapid Prototyping: Leverage the speed and flexibility of the FX10 and FX20 for prototyping. Early-stage prototypes can be printed with basic materials, while final production parts can include high-performance composites, allowing faster feedback cycles.
- Design for Composite Printing: Adjust your CAD models to capitalize on the unique properties of composite materials. This could mean redesigning parts to integrate support structures, reducing material mass, or including fiber reinforcement to increase stiffness in strategic locations.
- Consider Print Orientation: Orienting parts to maximize the benefits of fiber reinforcement ensures that the load paths align with the print direction, boosting the strength and reliability of the finished component.
- Still Need more Strength:The FX10 with the optional Metal Print capability. You can print all the materials and support processes of Markforged’s proven Metal X System on your plastic composite printer. The FFF style lightweight metal parts again allow every engineer to easily create strong light weight metal parts. No major facility updates required. Markforged bound the metal particles into a filament so it's safe. Material choices include 17-4PH SS, D2, H13, Inconel 625 and Copper. With 316 stainless steel on the way.
The Benefits: Time and Cost Savings, and Industry Leadership
Streamlined Production: The ability to print complex, composite-reinforced parts in-house reduces the dependency on external suppliers and speeds up the development cycle. With less lead time, companies can move from concept to market faster than ever before.
Innovative Design: Freed from the constraints of traditional machining, engineers can design more intricate, optimized parts that are stronger and lighter than ever. This fosters innovation and gives businesses an edge over competitors stuck in conventional production methods.
Cost Efficiency: By replacing metal parts with carbon fiber composites, companies can achieve significant cost savings in both material and labor. The FX10 and FX20 make it feasible to produce high-quality, end-use parts without the high price tag of conventional manufacturing.
Transform Your Production Today
Ready to bridge the gap between metal and plastic? Whether you’re looking to invest in a Markforged FX10 or FX20 for your operations or want to experience the power of composite printing through our services bureau, EXBuild is here to help. Contact us today for a printer quote or send over your part for printing—take the first step toward a stronger, more efficient production line.

Written by The EXBuild Team
The EXBuild Team of application engineers combined their depth of experience and industry knowledge to bring you the contents of this article.