As we covered in Physics of 3D Printing, imagine the fiber is like raw spaghetti. If you try to bend it, it snaps. If you try to compress it lengthwise by trying to push the two endpoints closer together, it also snaps. However, if you load it in tension by pulling on it, it can hold a decent load. Like the spaghetti, continuous fibers are strongest when loaded in tension. The key is understanding where the fibers are loaded in tension, and how a given load can distribute amongst the local fibers.
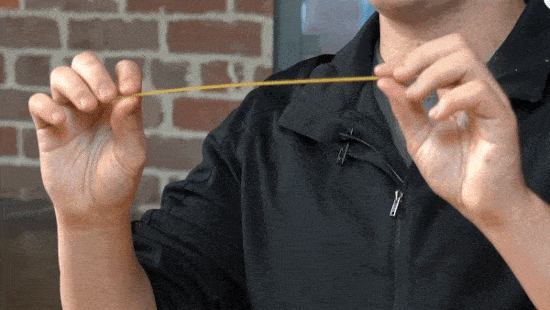
Types of Fiber Fill
Eiger, the Markforged 3D printing software platform, provides a few options for reinforcing your parts with continuous strands of composite fibers. Each reinforcement strategy can be applied to a layer or group of layers in a part. The different reinforcement options allow you to strategically place fiber so that you can optimize the reinforcement method for your part's loading conditions.
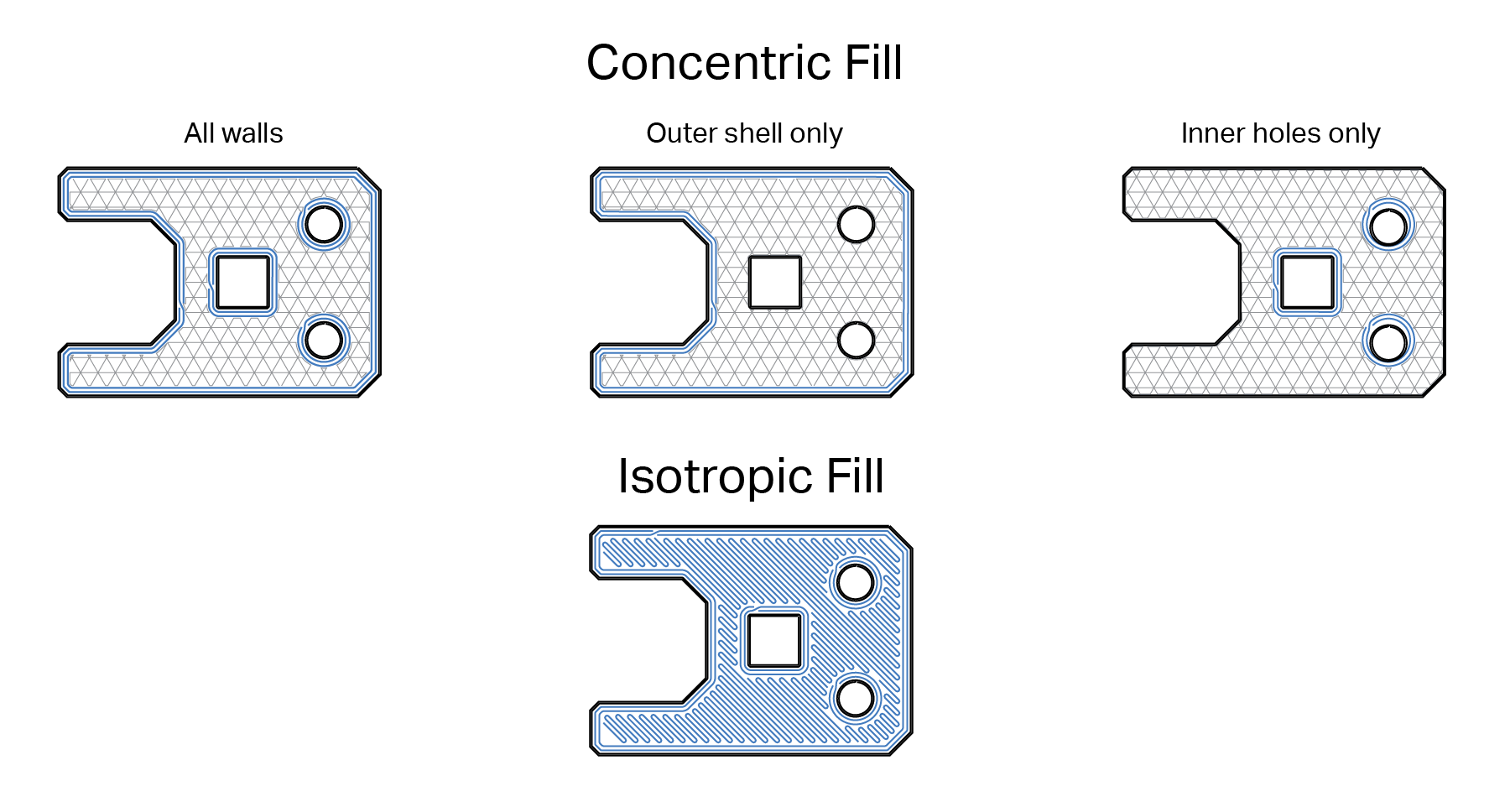
Concentric Fill
Concentric Fill lays fiber around the perimeter of a wall. This fill type mainly helps resist bending about the Z axis and strengthens the walls against deformation. You can specify how many fiber shells you want by changing the number of concentric fiber rings. You can edit the start point of the fiber by changing the "Start Rotation Percent" setting when viewing a 2D layer slice or group in Internal View.
All walls: This type lays down fiber to reinforce both the outer shell and the inner holes, providing the reinforcement properties of both.
Outer shell only: This type only reinforces the outer walls of a part. This can be used to reinforce the part for bending or impact loads applied to the sides of the part.
Inner holes only: This type only reinforces the inside walls of a part. This can be used to strengthen bolt holes or cavities to improve load distribution when compressive or out-of axis torsional forces are applied to inner holes.
Isotropic fill
Isotropic fill routes fiber back and forth in a zig-zag pattern to simulate the individual unidirectional layers of a traditional laminated composite. By default, subsequent isotropic fiber layers rotate the fibers by 45 degrees to achieve unidirectional strength within a fiber group, but the fiber angle (the orientation of the zig-zag pattern of the fibers) can be changed if needed. Layers of isotropic fill fiber resist bending in the XY plane. In addition to the isotropic fill pattern, this option by default traces concentric rings around all walls to improve wall strength.
Types of Fiber
Your choice of fiber impacts the behavior of your part. It can affect strength, stiffness, failure condition, and even heat resistance. Selecting the best fiber for your application is an important factor in your part's performance. Watch our webinar on selecting a fiber fit for your application, or check out or material data sheet for more.
Carbon Fiber
Carbon fiber has incredible strength to weight properties. It is a very stiff material that remains close to rigid until failure, in which case it often fractures or splinters. It's best used in constant loading conditions when you want to match the strength of metal at a fraction of the weight, since it behaves like 6061 aluminum.
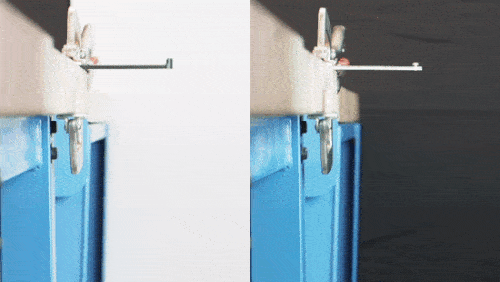
Fiberglass
Fiberglass is a robust reinforcement option that has a bit more flex and energy return to it than carbon fiber. It's best used in intermittent loading conditions, and bends until eventual fracture. Fiberglass is a great general-use fiber for when you need sturdy parts, and it is the most cost-effective reinforcement option.
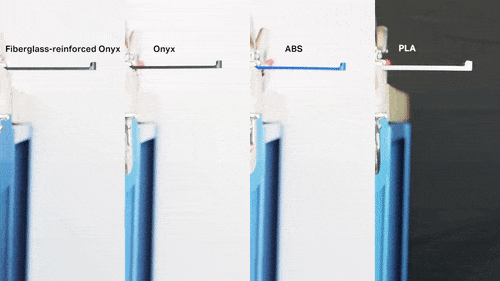
Kevlar
Kevlar is a very shock-resistant material ideal for impact loading or similar use cases. It is very tough, and will fail by bending until it eventually permanently deforms.
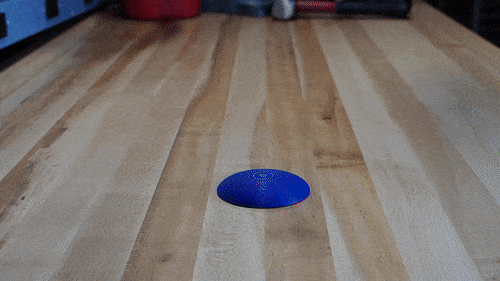
High Strength High Temperature (HSHT) Fiberglass
HSHT Fiberglass is a heat-resistant fiber reinforcement material. It has a higher heat-deflection point than the other fibers, meaning it can hold its strength at high temperatures. It is similar to fiberglass in that it has high energy return and will bend until it fractures.
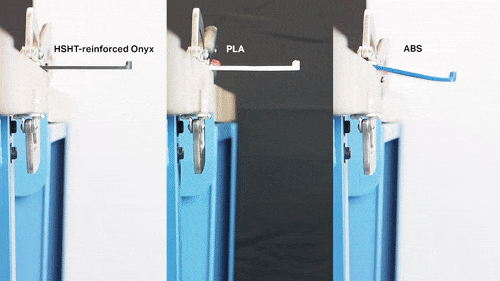
Reinforcing For Different Loading Conditions
Tension
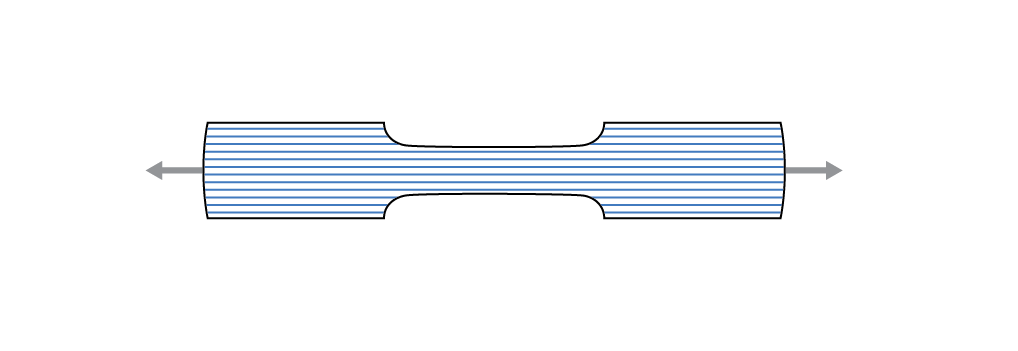
Fibers are strongest in tension, so a part loaded in tension should consist of fibers running up and down the length of the part, being “stretched” by the force. You can align fibers with your tensile forces with concentric rings along ribs or with isotropic fiber by setting the fiber angle parallel to the force.
Bending
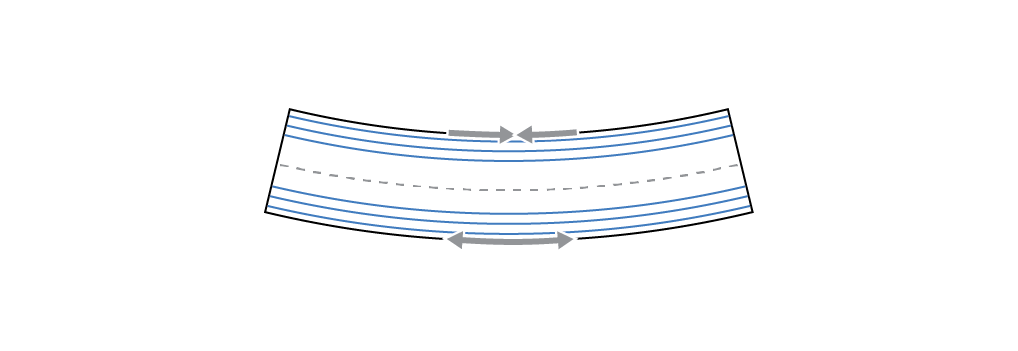
Beam Bending Theory shows that when a beam is bent, the inside face of the bend is loaded in compression, while the outside face of the bend is loaded in tension. By putting rigid materials on the extremes of a beam you reinforce it most effectively. This is why traditional composite layups consist of fiber panels on each face with a softer material on the inside, forming what is called a sandwich panel. To reinforce a part in bending, build a sandwich panel with isotropic fiber panels if the neutral plane is in XY, or concentric fiber when bending around the Z axis.
Compression
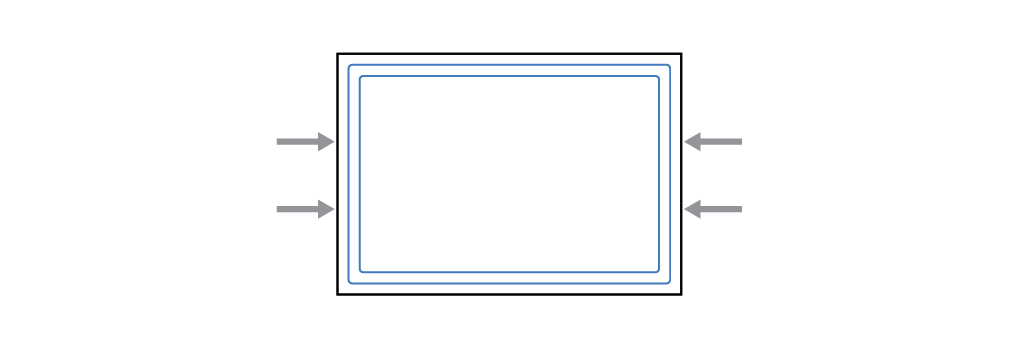
The key to dealing with compressive forces is in the force distribution. The fiber should serve as a scaffold beneath the load, able to distribute the load along the fiber’s path. Side loads can be reinforced from compression with concentric reinforcement. Vertical loads can be reinforced from compression using isotropic reinforcement on the upper and lower faces, and concentric reinforcement between the two Isotropic panels to further support the load. This is especially helpful for supporting clamping forces from bolts.
Fiber Anisotropy
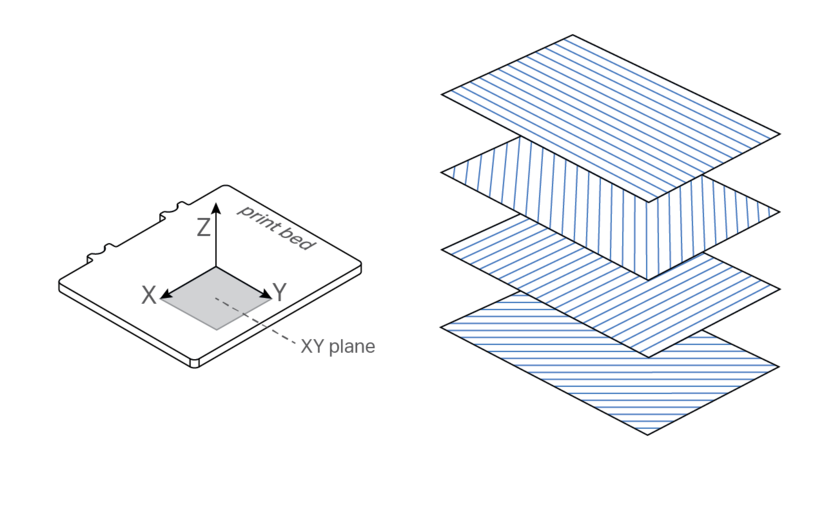
Markforged 3D printers print composite parts that are effectively transverse isotropic. While isotropic materials have uniform material properties in all directions, transverse isotropic materials have one set of properties along an axis, and a different set on planes normal to that axis. This translates to 3D printed parts, in which the part strength on XY planes is stronger than the part strength along the Z axis, especially with continuous fibers. This is why it’s important to consider print orientation during the design process.
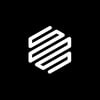
Written by Markforged
Markforged is transforming manufacturing by addressing 3D printing as a holistic problem. Their process innovations are only possible by a combined effort in advanced cloud computing, cutting-edge materials science, and industrial design.