At Markforged, our mission is to reinvent manufacturing. We obsessively focus on innovation at the intersection of precision engineered hardware, strong materials, and intelligent software. Our unique combination of core competencies and proven ability to deliver customer value will continue to accelerate the adoption of Additive Manufacturing, and reinvent manufacturing everywhere.
Blacksmith connects part design, production, and inspection with a powerful Artificial Intelligence (AI). This will reduce the cost of production, accelerate time to market, and reshape the industry as we know it. Our main motivation for Blacksmith is to provide engineers with tools that allow them to make anything they can imagine, and it’s this philosophy that drives our development, validation, and rollout decisions.
Blacksmith Today
Blacksmith includes a suite of features that will augment and automate manufacturing processes. These include:
Printer Calibration
When a new Markforged X7 is purchased, it has passed a rigorous systems level inspection at our manufacturing facility and is known to meet our high-quality standard. Markforged customers put their systems to work, hard. The X7 has been in production and deployed around the world since 2016, in some of the most demanding manufacturing environments. We have created a series of automated calibration procedures to ensure each and every printer is operating at the high standards required for Blacksmith. Some of these utilities are new and were developed specifically for Blacksmith in addition to the standard out-of-the-box setup utilities. When enabled, Blacksmith provides an easy-to-use utility which guides the user through the full range of automated calibration procedures.
In-Process Inspection
Blacksmith inspects parts while they print using the X7 onboard laser micrometer and patented scanning process. It intelligently generates a laser inspection toolpath at slicing time for your part and build settings. The resolution is controllable by the user, and allows for trade-off decisions to be made between scan density and print time. Once a part is configured and a build is locked in, a user simply presses the print button, and the printing and scanning process will be completed automatically.
As scan resolution increases, Blacksmith is able to gather more data during the printing process. This means Blacksmith can accurately measure smaller features, while also increasing the amount of time spent scanning during the print. Increasing scan resolution also allows for us to decrease the error of the mean for all part feature measurements, resulting in tighter scan accuracy reporting.
Automatic Quality Reports
Blacksmith automates the collection, upload, and registration of high fidelity in-situ measurement data. Blacksmith provides a range of intuitive visualizations that make part inspection simple, saves time, and ultimately improves manufacturing productivity.
Blacksmith provides a set of easy-to-use tools to view your part and scan data in 3D, as well as select critical tolerances in real-time. If you need a part feature to be within ±100 µm, for example, of the intended design, you can select that on the bar and all points above that will turn red so you can evaluate if the part is acceptable for your particular application. Users can also view a parts historical scan data right on this page, making traceability easy.
Where to use Blacksmith today
Blacksmith is a valuable tool for manufacturers today, here are some examples of challenges that can be fixed with Blacksmith.
In-process laser scanning
Get replacement tooling faster
A manufacturer currently procures go/no-go gauges from a vendor. These go/no-go gauges are inspected and verified by the vendor, but can take weeks to get in hand. These gauges often get misplaced or broken easily on the manufacturing floor and can bring production to a halt when not available. Blacksmith will allow a customer to print these gauges repeatedly and automatically verify the part on demand without waiting on a vendor. This will get the line up and running significantly faster.
Augment quality department resources
An engineer tasked with designing a specialized production tool last minute, but it has to go through a verification before being allowed on the line. The current workflow is for the tooling to go to a separate quality department which currently has a one week backlog. This delay is putting the final product’s ship date at risk. With Blacksmith, the design engineer can verify the part right off the print bed and get it to the floor faster.
Automated verification and traceability
A customer is making an end-use part that will be shipped to one of their customers. The end-customer wants documentation to ensure the part is meeting their specifications. With Blacksmith, the manufacturer can send the automated print report to give them confidence in the part. The print report is stored in Eiger and can be referenced at any future date. If a customer wants that part again, print reports can be compared to ensure that the parts are the same.
Final Thoughts
Blacksmith is the Adaptive Manufacturing Platform that will continuously evolve and expand in capability. Markforged printers are already in more than 10,000 facilities around the world and have collectively produced more than 10 million parts. Our technology is fundamentally driven forward by our ability to learn at the speed and scale of our global fleet.
Our team has been hard at work on Blacksmith for a long time, and we are excited to bring it to manufacturers all over the world. We have worked closely with customers and trusted industry partners to develop the core technology which powers this incredible product. Thank you to everyone who made Blacksmith a reality.
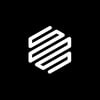
Written by Markforged
Markforged is transforming manufacturing by addressing 3D printing as a holistic problem. Their process innovations are only possible by a combined effort in advanced cloud computing, cutting-edge materials science, and industrial design.