Hangar One Avionics is a San Diego-based avionics, maintenance, repair and installation services provider with customers in airborne law enforcement, business aviation, and general aviation.
Oftentimes, specific customer needs will require unique and custom parts — such as a pilot-seat console. Until a few years ago, Hangar One Avionics built all of these custom and low-volume parts for customers through CNC machining, a traditional subtractive method of manufacturing.
Turning to Additive
Hangar One discovered that many of the parts that proved difficult to fabricate through CNC machining and other conventional manufacturing processes were strong candidates to be built through 3D printing. Incorporating additive manufacturing into operations made manufacturing of these parts significantly faster, as well as a much simpler and easier process from start to finish.
Using 3D printing to replace aluminum parts with lighter, equally strong carbon-reinforced composite parts led to significant weight improvements for helicopters that swapped metal parts with composites. For example, a composite part weighing five pounds less than the metal part it replaces translates into a customer helicopter equipped for five additional pounds of cargo, fuel, or extra lifting capacity.
Saving Time with Blacksmith
With AM, one time consuming aspect of the traditional manufacturing process still remained for 3D printed parts. Before parts could be used or installed in aircrafts, they had to pass through a rigorous full inspection. This manual process was time consuming — it required setting up appropriate test procedures, retrieving inspection equipment, and conducting the testing. On average, this took 30-45 minutes to complete for each part.
Hangar One estimates that using Markforged’s Blacksmith part inspection software saves 30 minutes per part on average. With Blacksmith, inspection is an automated process that works while the parts are printing. After each part is printed, reviewing the analysis and report only takes a few minutes.
In addition to making the inspection process both easier and faster, Blacksmith ensures that inspection data is available reliably for future reference because its data is stored in the cloud, rather than on paper. This is critical, due to traceability and FAA requirements for keeping aircraft part records over a long period of time.
Testing Blacksmith
Before Hangar One could introduce a formal change to the way it inspected parts, the company knew that it had to rigorously test the value of this new process to satisfy its own internal staff as well as its customers. This required verifying that Blacksmith had the level of accuracy and consistency that the company needed for aircraft parts.
After printing several parts with Blacksmith, the parts were also inspected with conventional measuring tools. When the two sets of data were compared, Blacksmith was found to be more accurate. Since then, Blacksmith inspected parts have consistently been accurate within 3-4 thousandths of an inch.
“Explaining why we use Blacksmith is simple. Blacksmith does the same thing that the old manual inspection process did. The difference is that Blacksmith digitizes the process which makes it faster, easier and more reliable.” - Matthew Roth, Head of Machining at Hangar One.
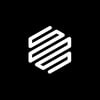
Written by Markforged
Markforged is transforming manufacturing by addressing 3D printing as a holistic problem. Their process innovations are only possible by a combined effort in advanced cloud computing, cutting-edge materials science, and industrial design.