3D metal printing technology — like metal fused filament fabrication (metal FFF) — presents a breakthrough way to make functional metal parts accessible for businesses of all sizes. Metal FFF and composite FFF share many key process advantages over conventional manufacturing.What are some of the applications that metal FFF is well-suited for? This blog post includes metal FFF application examples for 1.) concept models and functional validation, and 2.) workholding/alignment tools.
The following metal FFF application examples, while not an exhaustive list, can serve as examples to help manufacturers gain an accurate understanding of what’s advantageous to 3D print. Markforged recommends that manufacturers examine their own operation for similarities and opportunities to leverage advantages of metal additive manufacturing.
Concept Models and Functional Validation
Metal FFF printers are an ideal R&D technology — enabling users to quickly and efficiently check if their design intent meets functional requirements. Because metal FFF is fast and light on logistics, parts can be quickly printed and avoid long lead times common with conventional fabrication.
Within this space, prototypes are the most common application. They come in many shapes and sizes, but typically are most valuable when there is a need for a metal prototype for a metal part. Metal prototypes are required when the properties required in the prototype cannot be matched by composite parts. While many parts can be prototyped by metal FFF, the type of parts that have the highest ROI are ones that are economically inefficient to produce at low volume or are impacted by long lead times.
Bespoke parts. Low volume parts like custom impellers and nozzles can be prototyped and produced on a metal FFF 3D printer. The complex geometries required and the low volume nature of these parts fall under this application.
Cast parts. Die casting is a cost effective way to make complex parts at high volume. However, these parts are also extremely expensive to prototype. Metal FFF enables users to print near net shape parts to refine cast part design before committing to production tooling cost.
Custom CNC parts. Metal 3D printers provide a less costly and faster method than procuring parts from third party CNC manufacturers, and can materially augment internal fabrication bandwidth. CNC prototypes that are most impactful to print are typically complex and require more machining operations.
Workholding/Alignment Tools
Like prototyping, workholding and alignment are common CFR printing applications. Metal FFF adds a new dimension to the existing composites applications space, thus opening up new opportunities.
Composite tooling is transformational, but has its weaknesses. In these areas, metal FFF parts shine. Industrial 3D printer metal is both heat and wear resistant where composites are not.
Manufacturers can also utilize the inherent performance advantages of metal 3D printing, which include light-weighting, cooling channels, etc. — to build tools that perform better than the conventional alternative.
Hybrid Tools. 3D printed metal and composite parts can be combined into hybrid tools. These tools enable users to harness the inherent strengths of each technology. This includes instances particularly where localized wear resistance is required; for example, users can print metal tips and plastic bodies.
High wear End of Arm Tooling (EOAT). EOAT, which is a common composite application, has additional specific metal applications. Examples include:
- High wear surfaces where metal tools far outlast composite tooling.
- Tools that operate in heated environments and can work with hot components. Some EOAT is used in high temperature locations where only metal can reasonably operate.
- Smaller and more intricate EOAT that are too small or intricate for Continuous Fiber Reinforcement (CFR).
Brazing fixtures. Brazing fixtures need to be strong in high temperatures. Metal FFF 3D printing technologies meet these requirements and add a level of customizability. Metal parts can also work in the extreme heat conditions of furnaces. Complex features and difficult-to-machine materials make conventional manufacturing expensive.
High wear workholding (stanchions, cradles, etc). Line tools like stanchions and cradles are subject to repeated abrasion and wear. 3D printing metal parts provides an easy way to make customized tools with hardened, wear-resistant metals.
Thanks for checking out the EXBuild blog! For more information about how you can get started with additive manufacturing at your business, contact us today.
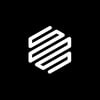
Written by Markforged
Markforged is transforming manufacturing by addressing 3D printing as a holistic problem. Their process innovations are only possible by a combined effort in advanced cloud computing, cutting-edge materials science, and industrial design.