Just as with any manufacturing process, there are optimized and non-optimized ways to design parts for 3D printing. In this case, DFM (Design For Manufacturing) becomes DFAM — Design For Additive Manufacturing — and while your printer won’t chastise you like your machinists will for failing to consider fabrication methods in your design, the part integrity will suffer. This article covers the general outline for printing a composite part on Markforged printers: design, reinforce, print. You might be surprised by how straightforward composite printing is!
Step 1: Design
Only in rare cases should a part be printed from the same CAD file as the machined design. Sure, you can print anything that will fit inside the print volume, but that doesn’t guarantee that it will perform as desired. Small modifications specific to extrusion printing, such as orienting a part differently on the build plate, can drastically improve performance. Designing with the manufacturing process in mind can often make the difference between function and failure.
The anisotropy of extrusion printing will guide many design decisions — since parts are built layer-by-layer, the X and Y axes (left/right and forward/back) inherently have more strength than the Z axis (up/down), which relies on adhesion between plastic layers, rather than the bonds within a plastic strand. For this reason, the ratio of Z-axis to X or Y-axis strength is about 70% in extruded parts. This is helped by the relatively small layer heights available on Markforged printers, but it is still a consideration for how the part is oriented on the build plate.
Combining this property of extrusion with the anticipated loading conditions, you should orient the part such that tensile forces are aligned with X and Y axes — so they pull along the filament, not between layers. Similarly, shearing forces should be constrained to parallel to the Z-axis, otherwise you’ll risk separation between layers.
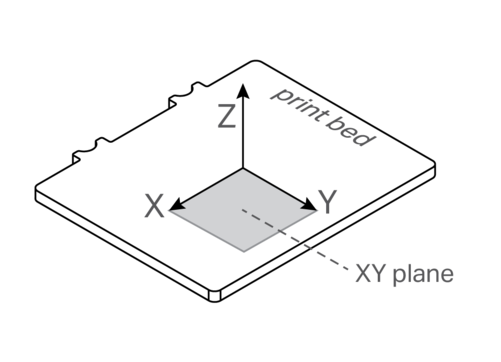
Before printing a part that is typically machined metal, there are two kinds of redesign that you might think about:
- Modify the part for the printing process itself, without changing the fundamental design. The updated part has the same geometry, but small adjustments have been made so that it can print well. This might include eliminating overhangs, chamfering edges, or filleting corners, then choosing bed orientation carefully so that supports are kept to a minimum and stresses are applied as described above.
- Modify the part to leverage printed strength. This is a much broader form of redesign, which looks at the loading conditions and reconsiders the overall geometry given the differences between subtractive and additive processes. Rather than leaving material where it neither hurts nor helps, with printing you do not need to add this material in the first place. You might orient the part such that loading paths are horizontal and therefore can be reinforced with embedded fiber. You can read more about these design strategies in our Composites Design Guide.
The second option is true design for additive: looking at a machined or cast part from a completely fresh perspective, taking the specific strengths of 3D printing into account.
Step 2: Reinforce
Once your part is designed for additive manufacturing, you can set it up in Markforged's Eiger software. This secure, cloud-based program guides you through part setup and reinforcement settings all the way to kicking off your print and monitoring it remotely. Eiger is included with Markforged printers, and you can also demo the software at Eiger.io. All slicing of parts is done on Markforged’s cloud servers, so you never have to worry about losing print data. For an in-depth overview of the reinforcement process in Eiger, watch this Eiger walkthrough video.
All reinforcement is handled in Eiger, so there is usually no need to adjust the CAD model to accommodate fiber. However, you can design your part with reinforcement in mind. This means choosing a print orientation (which will dictate the fiber plane) and making sure your features are large enough to fit the fiber you need in them. More details can be found in our Composites Design Guide. When reinforcing specific layers with fiber, you can choose between two fiber fill patterns you can specify: Concentric and Isotropic fill.
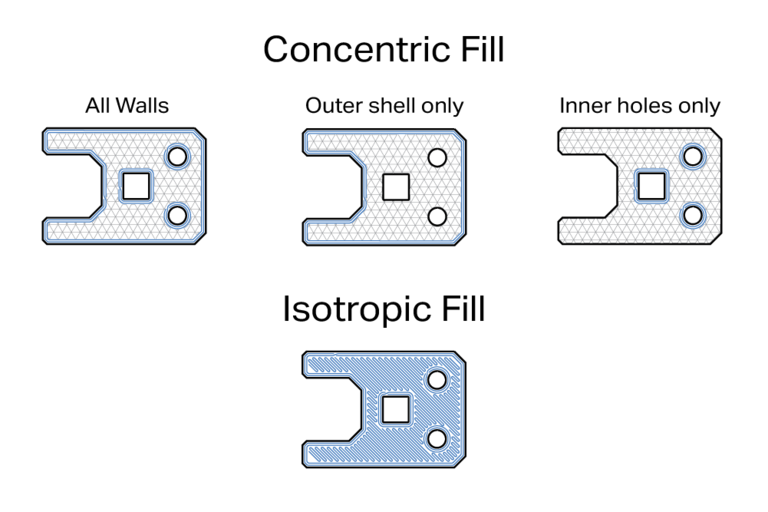
Concentric fill puts fiber around the walls of the part, with the plastic comprising the infill matrix as usual. The user may reinforce only the outer shell — useful for bending or impact loads — the inner holes or cavities — ideal for load distribution from compression or off-axis torsion — or both outer and inner. Eiger allows you to specify how many layers receive fiber, and the number of concentric rings within each layer.
Isotropic fill routes fiber back and forth in a zig-zag pattern to simulate the unidirectional layers of a traditional laminated composite. This pattern also incorporates concentric fill for wall strength. By default, subsequent isotropic layers rotate the fibers by 45° to achieve unidirectional strength within a fiber group, but this fiber angle can be changed if needed. Think of isotropic layers like the top and bottom of an I-beam: they resist bending in the XY plane.
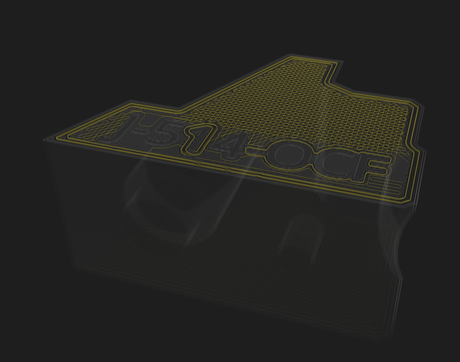
Depending on your part's loading conditions and geometry, you can choose groups of layers or individual layers to reinforce with either of these reinforcement settings. This level of granularity allows you to control how and where your part is going to be strong, to optimize it for its loading conditions.
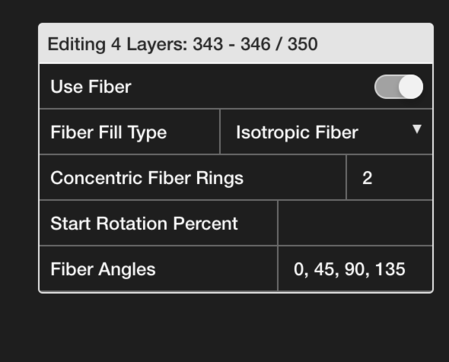
Once your fibers are set up the way you like them within your part, you can add your part to a build of multiple parts with like materials and kick your part off to a printer connected to your Eiger organization. Only users within an Eiger organization can send files to printers within that organization, so the program keeps all your files secure for your business.
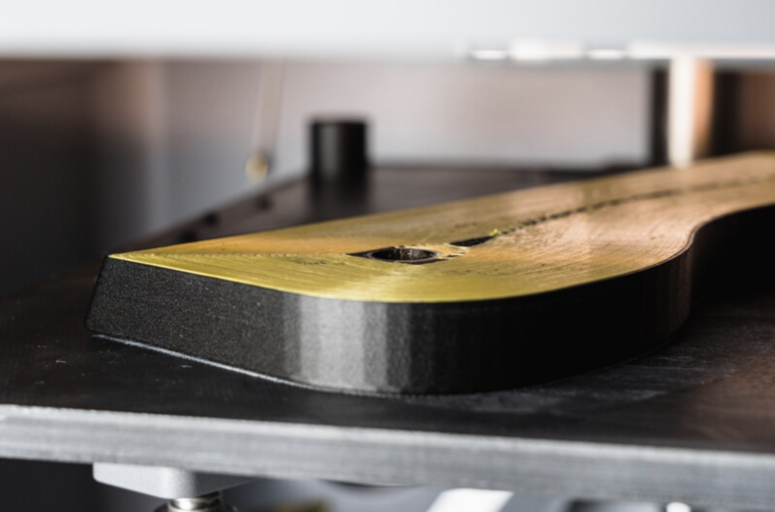
Step 3: Print
Once you’ve verified that the build plate is clear and you’ve sent the file to the printer through Eiger, the print sequence begins. The matrix plastic material is largely hollow, forming a "shell" of plastic with infill within the part to connect and support the walls and fiber strands:
- The printer downloads the file locally, in case it loses online access.
- Industrial printers (X3, X5, X7) will first laser-scan the bed and compensate for any height deviations in the first few layers. Desktop series printers may need to be leveled beforehand.
- The printer heats up and purges several inches of filament to ensure a high-quality first layer.
- The printer will begin with four solid-fill floor layers (unless user specified a different number in Eiger), before it starts printing infill and walls.
- The print proceeds with walls and infill until four layers before the first fiber layer.
- Before a group of fiber layers, four solid floor layers provide a foundation for the first layer of fiber.
- Within each layer that has fiber, the fiber gets ironed down first, and then the plastic walls and infill.
- One solid floor layer closes the fiber section, and the walls-infill pattern resumes.
- This pattern continues until the part is complete, with supports applied underneath any overhangs.
Once the part is complete, you’ll get an email notification. Just remove the build-plate, carefully pry the part off the print bed, peel away any support material, and your composite part is ready for use!
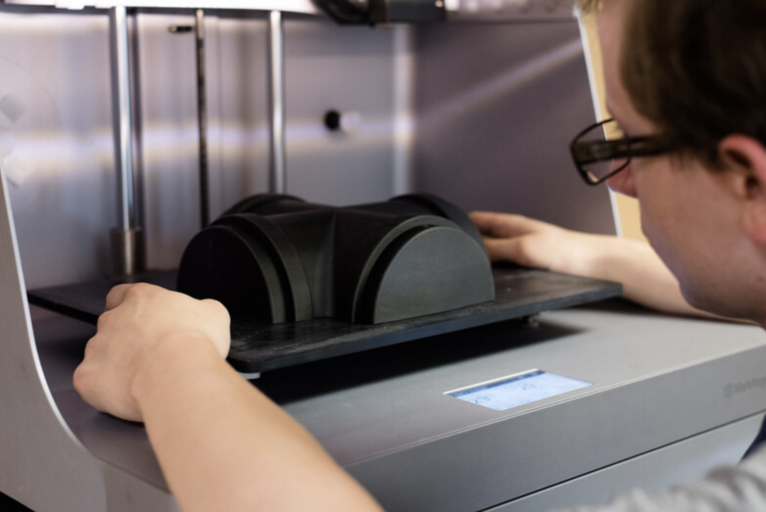
By now you can probably tell that the potential applications for composite parts are limitless. By leveraging the strength of continuous fibers, Markforged Desktop and Industrial Series printers can produce stiff and durable parts at previously impossible speeds. If you use custom fixtures or require machined parts for your manufacturing process, it’s likely that printing can streamline your workflow by reducing lead-time for replacements, cutting material costs, and improving iterability. Companies who learn to incorporate printed composites regularly report a return on investment for the printer in weeks or even days.
If you’re interested, get in touch with a Markforged Applications Engineer to see how you can leverage metal-strength composite printing.
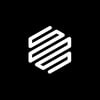
Written by Markforged
Markforged is transforming manufacturing by addressing 3D printing as a holistic problem. Their process innovations are only possible by a combined effort in advanced cloud computing, cutting-edge materials science, and industrial design.