Every additive manufacturing company says that their latest product offering is “groundbreaking” and “revolutionary”, which can get a little tiresome and make it difficult to really understand if any AM technology will actually make a positive impact for your business. With the recent launch of the M600 from Meltio, the loft promises of a groundbreaking technology are still there, BUT I believe there are six unique aspects of this machine that will help it deliver real value for those who need to produce metal components.
1. Second gen for the win
Purchasing the first generation of any technology comes with a some amount of risk, as it often serves as a proof of concept, revealing both strengths and weaknesses. However, a second generation of a product allows a company to refine its design, address the shortcomings, and enhance the overall performance based on user feedback and technological advancements. The Meltio M600 is a prime example of this evolutionary process. With the lessons learned from its predecessor, the M450, Meltio has developed the M600 to offer unparalleled capabilities in metal additive manufacturing.
2. Advanced Laser-Wire Deposition Technology
The laser-wire deposition technology in the M600 received some key upgrades to make it extremely capable and robust. The switch to lasers that emit blue light means that this new deposition head can weld a wider range of materials including copper, aluminum alloys, and marine bronze.
These blue lasers are now integrated directly into the deposition head. This provides factory calibrated precision alignment without the need for manual calibration by the end user. Another benefit of this arrangement is the elimination of fiber optic cables, which add complexity, cost, and added maintenance. This results in high-quality, consistent prints with minimal calibration.
3. Fully Inert Chamber for Optimal Material Properties
The M600 features an inert chamber with an oxygen content of just 20 ppm, ensuring the best possible material properties during the printing process. This low oxygen environment is crucial for maintaining the integrity and performance of sensitive metals, reducing oxidation, and enhancing the mechanical properties of the printed parts.
4. Enhanced Productivity and Efficiency
Meltio's M600 is designed for high productivity, boasting a 60% increase in efficiency compared to its predecessor. Key elements contributing to this boost include:
- High Deposition Rates: The hotwire feature significantly increases deposition rates, making the M600 ideal for large-scale production.
- Minimal Downtime: The M600 is engineered for high uptime with features like automated material sensing, a pneumatic wire cutter, and robust wire feeders, ensuring continuous operation with minimal maintenance.
5. Large Workspace in a Compact Footprint
One of the standout features of the M600 is its large build volume of 300x400x600 mm, capable of producing parts up to 150 kg. The machine has a compact footprint, making it suitable for machine shops with space constraints. The design maximizes efficiency without compromising on the size of the components that can be manufactured.
6. Intuitive and Future-Proof Software
Meltio has equipped the M600 with sophisticated software solutions to streamline the printing process and enhance user experience:
- Meltio Horizon 1.4: This latest version of the Horizon software includes new features tailored for the M600, providing a user-friendly interface for 3-axis printing.
- Meltio Dashboard: A web-based cloud platform for monitoring and managing print jobs remotely. This feature enables engineers to oversee operations from anywhere, ensuring seamless workflow and immediate troubleshooting.
- AI-Driven Applications: The M600's infrastructure supports future AI-driven applications, promising continuous improvement and adaptation to emerging technological trends.
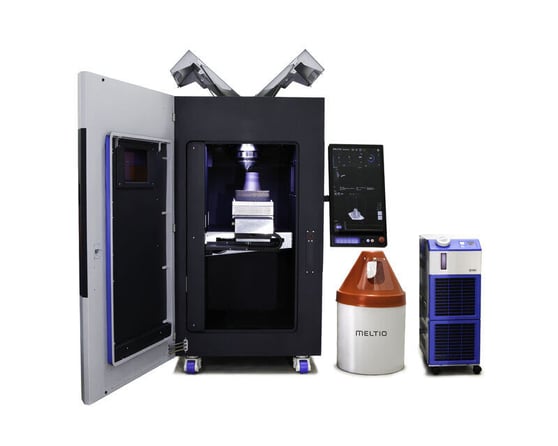
7. Robust Build and Maintenance
The M600 is built with high-quality servo motors and ball screws, ensuring reliable performance and minimal maintenance. Key design aspects include:
- Vision System: Equipped with three process cameras, the M600 offers enhanced monitoring and control during the printing process.
- Servo Motors and Encoders: Full linear encoders and high-quality servo motors ensure precise movement and print accuracy, even allowing print resumption in case of power loss.
- Zero Point Clamping: Most metal printed parts are going to need post processing and with the Zero Point Clamping system parts can seamlessly transition from the M600 into other manufacturing processes. Which enhances the printer's integration into hybrid manufacturing setups.
- Touch Probe: These features enable precise part location within the workspace and facilitate easy part exchanges.
8. Competitive Cost Efficiency
Despite its advanced features and high performance, the M600 is competitively priced. The use of off the shelf metal wire feedstock offers you an extremely low cost per kilogram of printed material. This affordability, combined with its productivity and versatility, makes the M600 an attractive option for businesses looking to integrate metal additive manufacturing into their operations without a prohibitive initial investment.
Conclusion
The Meltio M600 3D printer is a significant leap forward in the field of metal additive manufacturing. Its combination of advanced laser-wire technology, a fully inert chamber, enhanced productivity, a large but compact workspace, intuitive software, robust build, and competitive cost efficiency positions it as a powerful tool for modern machine shops. I believe the M600 will be a valuable asset, capable of meeting diverse manufacturing needs with precision, reliability, and efficiency. Meltio's commitment to innovation and quality ensures that the M600 is not just a product of today, but a cornerstone for the future of metal 3D printing.

Written by The EXBuild Team
The EXBuild Team of application engineers combined their depth of experience and industry knowledge to bring you the contents of this article.