The Markforged Metal X additive manufacturing process combines metal injection molding (MIM) and fused filament fabrication (FFF) technologies together into Bound Powder Extrusion. BPE provides a simple, cost effective way to create metal parts. The process closely mirrors conventional 3D printing with two extra steps -- washing and sintering.
Slicing
Just like plastic printing, all metal 3D printed parts start with an STL. This solid body file can be exported from any CAD program or created with a 3D scanner. After uploading this STL to Eiger (our cloud slicing software), you can orient the part by clicking on a face to mate it to the build plate. Once you select your orientation and the metal you would like to print with, Eiger slices your part. In this process, Eiger alters your part in four ways for printing.
Automatic scaling: To account for the uniform shrinkage in the part, Eiger automatically scales the part up by approximately 20%.
Open cell infill: Eiger automatically generates triangular open cell infill for all parts. These parts have floors and roofs (tops and bottoms) and walls (sides) that constrain the open cell infill.
Supports: Eiger automatically detects overhung surfaces and generates supports printed in metal underneath them. Eiger also generates a ceramic material release layer between the part and supports, allowing parts to be removed with the light tap of a hammer.
Raft: Underneath both the part and the supports, Eiger generates a raft. This ensures that the part will not warp during printing and shrinks properly during sintering. It also has automatically generated text that identifies the printing material.
A green (not sintered) printed part showing the supports and raft, release layer, and the actual part.
Once you slice your part, you can combine it with other like-material parts in a build. Multi-part builds are not necessary, and should only be used to optimize print times. Printing more parts increases the odds that a print will fail. That being said, builds can be an awesome tool to optimize printer bandwidth by allowing you greater control over the print time. For example, combining a part that takes 16 hours to print with one that takes 7.5 hours to print gives you a build that will take just less than a day, allowing you to easily cycle the build at the same time every day.
Printing
The Metal X prints parts layer by layer in the exact same way as conventional FFF 3D printing. It always uses two materials: a bound metal powder filament and a ceramic release material. The machine prints supports and the main part with mound metal filament. Ceramic release material is only used in the interface between the part and the support/raft, to allow for easy separation of the support/raft after sintering.
The core additive manufacturing process is similar for metals (top) and composites (bottom)
There are a few small differences between the Metal X printing process and the Markforged plastic/composite printing process.
The chamber and print bed are heated and must be brought to temperature before operating the printer. In addition, bound metal powder filament is brittle at room temperature and must be warmed up in the heated chamber before loading. Bed leveling on the Metal X is fully automated. This removes the most labor intensive and failure prone aspect of most FFF printers. The machine uses vacuum-held disposable print sheets that are replaced after each print. These sheets improve bed adhesion and make handling the fragile printed parts easier. Removing a part from the print bed is as simple as disabling the vacuum, taking the print sheet off with the part still attached, and easily peeling the print sheet off the part. After printing, the next step is to debind the part the Markforged Wash-1.
Washing
Washing is the simplest part of the Metal X 3D printing process. The Wash-1 is a heated debinding system that circulates Opeteon SF-79 around parts to break down the polymer binding material.The solvent dissolves most of the binder material throughout the entire part by penetrating deeper into the part as it removes more polymer. After washing, the part is in “brown part” form: more fragile than a green part, but still bound together by the last of the polymer. Wash time is automatically calculated by Eiger, and parts can be batch washed or washed sequentially -parts can be inserted and removed at different times.
The Markforged Wash-1 has a solvent bath that parts are submerged in while the polymer binder is debound.
Wash times depend on part size and wall thickness. It’s impossible to over-wash parts, so it’s ok to leave them in longer than their minimum time. After parts are washed, you transfer the parts into the drying bin of the Wash-1, where they are air dried to be cleared of solvent before sintering.
Sintering transforms a part from lightly bound metal powder to a full metal part. The part is heated from room temperature to around 85% the metal’s melting point in a blend of inert and mixed gas, then slowly cooled down. In the early stages of the temperature ramp, the furnace burns away the remaining binder through the tiny channels created by the washing process. As the temperature reaches its peak, the part shrinks about 17% to its final size while the ceramic supports turn from filament to dust. The machine slowly cools from its peak temperature until it’s safe to remove from the furnace.
The Markforged Sinter-1 turns printed and washed parts into metal.
The Markforged sintering furnace is designed to be intuitive to operate. To load parts into the machine, you place them on sintering furnace setter tray, load the tray into the Sinter-1, and seal the machine. You can sinter as many like-material parts as you can fit on the sinter tray (we recommend spacing the parts out slightly to make sure that they can shrink without touching each other). After sealing the machine, use the touchscreen to select the material to be sintered and start the run. A run takes a little more than a day (~25 hours) and varies based on the material being sintered. After sintering, parts are ready to go as soon as the process ends.
After sintering the part, you can remove it from its supports and raft. Depending on part geometry, this may require some force or hand tools. Sintered parts are fully metal and ready to use, but can also be post processed to improve mechanical properties, surface finish, or part accuracy.
Post Processing
Metal X printed parts can be post processed in most of the same ways that normal metal parts can. However, there are three methods that are more common than others:
Heat Treatment
While parts are usable right out of the sintering furnace, many Metal X printed parts require heat treatment to improve strength, stiffness, elongation, and hardness. Heat treatment processes vary from metal to metal -- we recommend following the ASTM certified heat treatment strategies mentioned on our material datasheets. These heat treatments can be performed in most standard furnaces, though Markforged sintering furnaces are not currently equipped to heat treat parts. Heat treatment also allows you to “customize” the qualities of a part -- by changing the parameters of the treatment, you can optimize the same base material for different use cases.
Post Machining
For precise parts like molds, post machining is a critical step in hitting tight manufacturing tolerances. Markforged parts can be surface machined, though you can only remove as much material is in the floor/roof or walls of your printed part. After machining, these parts can achieve mirror finish and the tight tolerance that one would expect from a standard machined part.
To achieve superior surface finish, parts can be post machined after sintering.
Sanding/Polishing
Sanding or polishing printed metal parts can improve surface quality to near mirror finish. Metal X parts a, with the same constraint as post machining: you must be careful not to remove too much material in the sanding or polishing process as it risks blowing through the outer shell of the part.
Thanks for checking out the EXBuild blog! Make sure to subscribe down below to have more 3D Printing and Additive Manufacturing content like this delivered straight to your inbox!
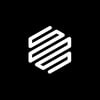
Written by Markforged
Markforged is transforming manufacturing by addressing 3D printing as a holistic problem. Their process innovations are only possible by a combined effort in advanced cloud computing, cutting-edge materials science, and industrial design.