In the ever-evolving world of additive manufacturing, innovation often comes in the form of subtle but revolutionary breakthroughs. Meltio’s dual wire printhead technology is one such innovation, redefining the standard for material handling in 3D printing. Two independent wire feeds allow material to be deposited smoothly without compromising the integrity or quality of the print.
In this blog, we will take a closer look at Meltio’s dual-wire system and explore how Meltio technology is pushing the boundaries of what is possible in additive manufacturing.
Dual Wire: Adding properties where it matters
First, it is worth clarifying in brief what is meant by Dual Wire 3D Printing in Meltio, which enables the printing of two different materials in a single print.
Through this Meltio’s technology, which fulminates the deposited material layer by layer, we have the ability to selectively adjust the properties we are interested in, by modifying the design, preceded by calculations of the forces that support the part. Once we have analyzed the loads and stresses to which the part will be subjected, we derive a design with a series of characteristics that optimize the topology.
For example, in relation to dual material, we can tell you that a significant number of parts manufactured with Meltio 3D printing have been made using the cladding technique, which could be defined as a technique that covers the sample with a surface layer that coats its geometry with a different material and insulates the sample, giving it new properties.
Our aim with this is to add an outer layer to a part to impart additional properties, as the base part material lacks the necessary characteristics for certain applications. In many cases, these beneficial properties are high hardness, corrosion resistance, or simply to fulfil a reconditioning function. An example to illustrate this would be a construction steel with limited corrosion resistance properties and with our technology, we overlay an additional layer of another material with excellent anti-corrosion properties. In this way, we are able to insulate the material from external corrosion.
A screw compressor case
An example of this is the screw compressor where cladding has been used to enhance the part. Anyway, we tell you how it is made and how it differs from other traditional manufacturing methods.
A female steel screw compressor is a type of screw compressor used in various industrial applications such as mining, chemical, petrochemical, food and beverage industries. This compressor is highly efficient and consists of two interlocking screws that rotate in opposite directions inside a casing. One of the screws has a female shape and the other has a male shape, allowing the two screws to move in a rotating action, pushing and compressing the air or gas that is between them towards the compressor outlet.
Female screw compressors are often made of stainless steel due to their high strength and durability and are commonly used for applications that require high-pressure compressed air or gas flow.
Conventional manufacturing methods for screw compressors include cutting, forming, and welding stainless steel sheets to create the compressor housing and parts. CNC machining is also used to create precision parts for the compressor. However, these manufacturing methods are often labor-intensive, expensive, and can generate a significant amount of material waste.
However, by utilizing Meltio technology, the manufacturing process can be significantly improved. Complex geometries and shapes can be produced with customizable designs that cater to specific customer needs. This process allows for faster production runs, reduced manufacturing times, improved product quality, and reduced material waste. Additionally, the process offers the ability to produce unique or limited-edition models while preserving mechanical properties comparable to those produced by traditional manufacturing processes.
Adaptability of complex geometries thanks to Meltio’s Design Guidelines
On many occasions, the optimization of a part is sought; however, it is important to note that not all parts are susceptible to optimization, nor is it in all cases of interest to optimize them.
Therefore, in the process of creating a part, depending on the type of part, topological optimization is often required before printing, ultimately seeking to reduce its structural weight while preserving the fundamental mechanical characteristics of that specific part, without affecting performance or efficiency under significant loads.
Through Meltio technology, we have seen advantages. To begin with, once we receive topological optimization, these designs are often complex because they have geometries and angles that are difficult to manufacture not only by traditional methods, but also by 3D printing technologies themselves.
At Meltio, once we receive the optimized part, we use our Design Guidelines to ensure that we can obtain the best quality when manufacturing it. An example of this could be reducing part angles to improve the printability of the part or for example modifying parameters to achieve lower roughness, without necessarily resorting to machining or minimizing the need for machining.
Advantages of using Dual Wire
Different alloys
Many parts produced using Meltio technology can incorporate high-cost, cobalt- and nickel-based alloys, which provide extra functionalities to the parts, such as could be improved mechanical properties. At Meltio, we have tested different combinations of materials, thus providing different properties to those of their base metals, such as greater resistance to corrosion, wear, etc.
Cooling channels
A part such as the Die Punch has particular advantages that we have achieved by using our technology. Our layer-by-layer manufacturing technology allows us to incorporate complex cooling channels, which are vital for efficient heat dissipation during operation of the part. In the case of Die Punch, a part that has formed internal cooling channels and, in contrast, powder manufacturing is problematic.
The difficulty is that, when using powder, there is a high probability that the powder will be trapped inside the cooling channels, creating a persistent blockage. Removing the powder from these channels can be extremely difficult, affecting the efficiency and functionality of the part. With Meltio technology, this risk is eliminated, as the cooling channels are not clogged. The risk of dust clogging is avoided, avoiding the need to use dust filler.
Versatility
When we talk about versatility, we can refer to the versatility of our technology and its applications. For example, versatility could refer to the ease of changing from one material to another, the fact that parameters can be easily modified with the use of the specific software offered by Meltio to take the user experience to other levels, the wide range of materials offered by Meltio, among numerous other advantages known to anyone who uses our technology.
Parts manufactured with Meltio technology offer remarkable advantages, starting with their ability to manufacture complex geometries, an achievement made possible by our advanced systems. These parts, intended for a variety of industrial applications, can adopt solid or hollow configurations, with one or two perimeters, providing flexibility according to the user’s preferences.
This versatility also applies to the ease of giving different metallic properties to the same part, by which we mean the use of dual materials that many of our parts feature. This capability allows for applications such as hard-facing or anti-corrosion coatings. It offers an easy, fast, convenient, and sustainable solution for multi-material 3D printing, without the risk of cross-contamination of the feedstock.
As an example of the advantages derived from the use of dual materials, we can consider the possibility of incorporating high-strength components in specific sections of a part, while other areas can benefit from materials with improved thermal conductivity. In short, a material selective approach is used to enhance the functionality of specific areas of the part.
Another very significant example, on 3-axis manufactured parts, is the use of supports and rafts. Supports are temporary structures that are added to areas of the part that have overhangs, protrusions or complex geometries. They prevent these sections from collapsing during printing. Supports are printed together with the part and are removed after processing by post-processing procedures such as cutting or sanding, although we always try to use as few supports as possible.
Rafts are additional layers of material that are printed underneath the part, providing a flat, stable surface for the part to rest on during printing. The rafts are especially useful to prevent damage to the part when removing the printing plate. In addition, they also prevent deformation due to heat during printing of materials or diffusion of elements from the base plate to the final part. Like the supports, the rafts are removed after the process.
Having said that, it is interesting that these supports and rafts are made of materials that, although compatible with the material of the part, are of lower cost as they will be removed and discarded from the final part.
Therefore, we will limit ourselves to using materials with specific properties in particular areas, especially in those critical sections resulting in multi-metal parts. For example, when using Nickel 625in the internal part of a pipe, despite being a more expensive material, its remarkable corrosion resistance surpasses that of Stainless Steel 316L, which is applied exclusively in the structural section of the pipe.
Dissolution and Heat Affected Zone
Meltio’s laser process produces an extremely compact heat-affected zone (HAZ), minimizing heat transfer to the layers below or the surrounding area of the melt pool. This results in a better microstructure of the printed part.
A common problem with other technologies is the tendency for the added alloy to mix significantly with the base material because it becomes diluted. In contrast, our technology is characterized by controlled energy input and low dissolution rates. This is especially advantageous in cladding applications, where the low dissolution rate preserves the integrity of the base material. If too much material is diluted on the base surface, the concentrations of the alloying elements change and there is a loss of part properties.
In the same vein, it is important to mention that our dissolution rate has advantages, such as the low formation of intermetallic compounds, known for their brittleness. Intermetallic compounds can break with very small deformations as they are highly fragile, and even residual stresses from printing can cause them to fracture.
With Meltio, the generation of intermetallic compounds is minimized. An example would be a test conducted in-house at Meltio, in which an SS304L steel base was bonded to a Ti64 impression using a silicon bronze interlayer. Iron and titanium are chemically incompatible when welded together, so the silicon bronze layer is necessary to make the bond possible. These materials did not melt together, but have been joined together avoiding the formation of brittle intermetallic compounds and creating a strong bond.
Near Net Shape
In terms of parts and final quality, parts manufactured with Meltio have more than 99.9% density. This high level of density guarantees the uniformity of the material throughout the part, eliminating any possibility of areas prone to breakage. In addition, problems such as lack of fusion are avoided and defects due to fatigue or tensile stresses are minimized, contributing to the integrity and durability of the final product.
The results show that samples printed using the Melt-wire laser metal 3D printing process perform at the same level as samples produced using conventional manufacturing methods. The results show low deflections and near-isotropic properties even in the as-printed state without the application of heat treatments.
Conclusion
In summary, Meltio technology offers a number of outstanding advantages, such as the ability to deposit material on pre-existing parts, high density, efficient deposition rate, large build volume, cost-effectiveness, almost unlimited part geometries, versatility in material choice and significantly reduced thermal distortion.
The resulting parts can therefore be adapted to a variety of applications and uses due to the diverse mechanical properties that can be achieved.
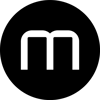
Written by Meltio
Meltio takes metal 3D printing to the next level by developing high-performance, affordable, and easy-to-use metal 3D printing solutions.