Awhile back we had a customer reach out asking us to help create a failure point in a part for a robotic application. At their facility they manufacture custom robotic lines that are manually loaded with dissimilar parts by operators. Occasionally a part fixture is loaded incorrectly, it would then cause a collision between part and robot arm or EOT. When this happened, it could lead to major downtime dependent on what collided. The operators had to wait while maintenance determined what was broken. Then if we have the necessary parts and a service technician to repair it.
The Process
The goal was to re-engineer a part that was strong enough to work under normal conditions, but fail if there was a collision protecting the robotic arm and EOT. With the new design a technician would know the exact procedure to replace that part, getting the machine up and running faster.
The first part was engineered to have CFR of carbon fiber, a patented process by Markforged. After running the part through simulation, the new design was as strong, if not stronger, than the original metal component. We didn't want that as the overall goal was to create a part with a controlled fail point. We made minor geometry modifications and removed all the CFR, and after running it through simulation it now reported we had the part strength our customer was looking for.
Utilizing just Markforged’s Onyx material with CCF, we were right at the minimum threshold needed. After printing a few tests parts and sending them over for internal review, they were ready for field testing at a customer’s facility. The new part ended up working exactly as intended and saving them time and money with a much more predictable fail/repair schedule. Who wouldn't want less down time and a less expensive repair? On minor collisions the EOT could just be snapped back on and continue operation.
Part slicing orientation
Review of infill and wall count
Simulation anchor and load force definition
Simulation results for original part
Actual printed part
Results
Fail point worked exactly as intended, but could we make it stronger?
After several months in operation with several customers they shared pictures of the part working exactly as designed and the failure damage when a collision occurred. They were curious if we could make it just a little stronger to increase uptime.
Original part after failure
Back to MF Eiger and Simulation we went. The challenge being, can we keep the deflection close to the same but add some strength. Using the exact same model, we changed the wall count and floor and ceiling count. Reran simulation just to make sure everything was still within parameters and boom; within 15 minutes we had a new version for production to review and authorize. It was in the mail the next day for field testing at their facility.
Review of infill and increased wall count
Simulation results for new part w/increased safety factor and minimal deflection change
Are you interested in learning more about how Markforged and how 3D printing can help solve similar problems? Visit our product page or send us a part you'd like to see printed.
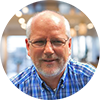
Written by Kevin Bork
Kevin is the Sr Manufacturing Specialist here at EXBuild. With over 30 years of manufacturing experience, he helps customers overcome any obstacle they might face in their production and design process. In his free time he enjoys playing billiards with friends and volunteering at his church.